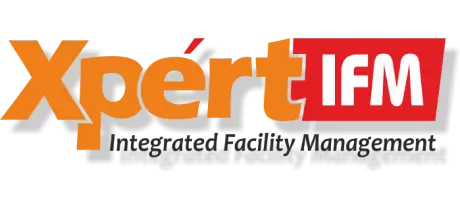
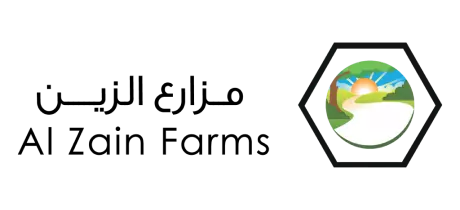
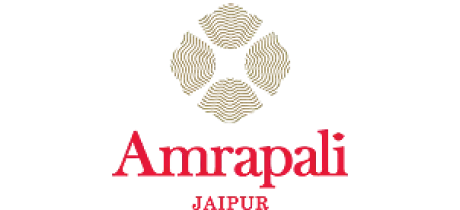
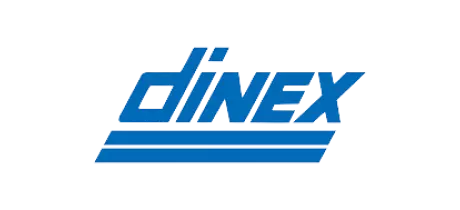
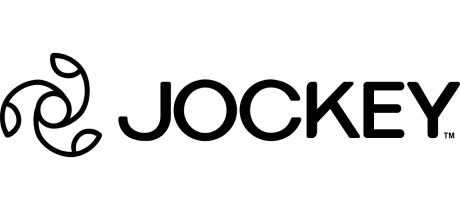
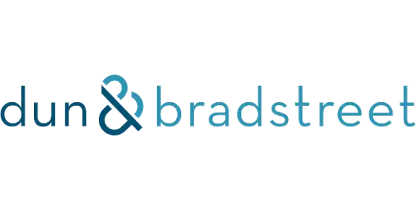
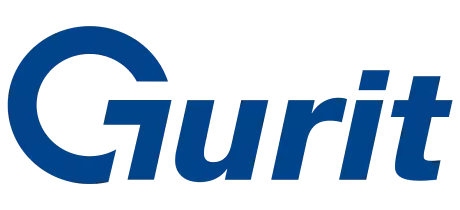
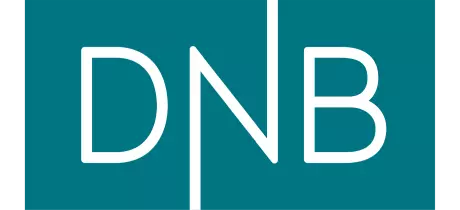
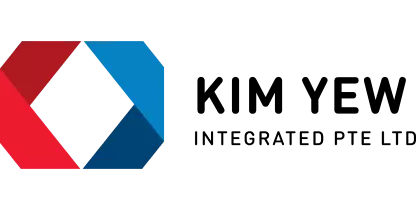
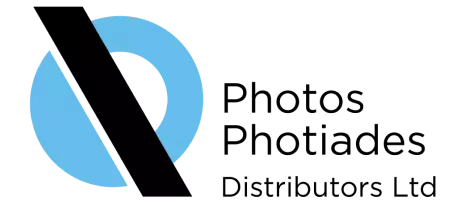
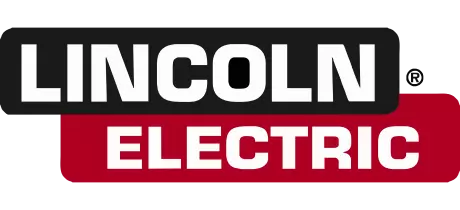
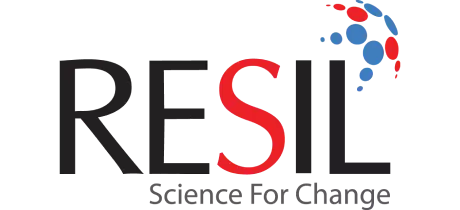
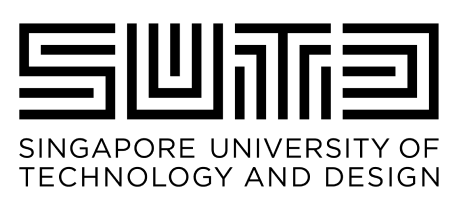
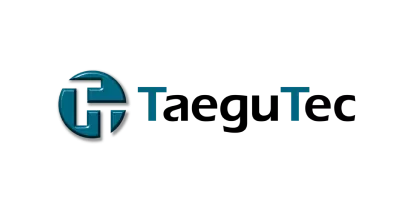
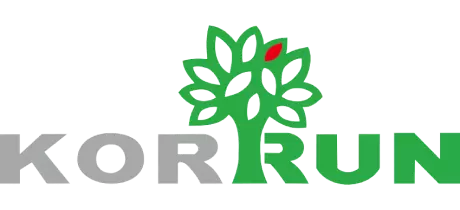
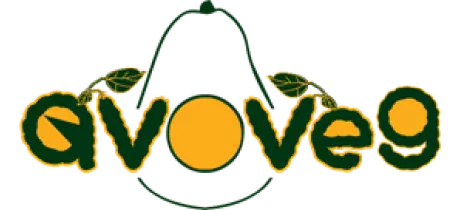
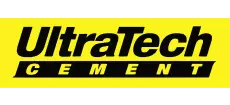
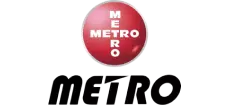
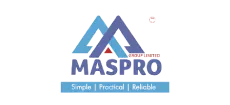
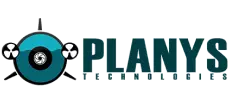
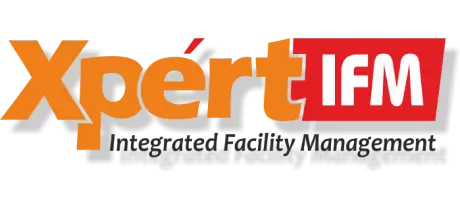
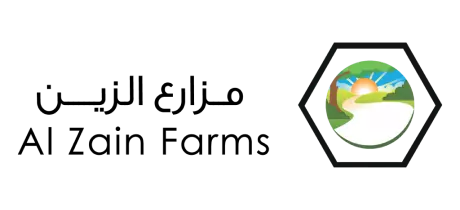
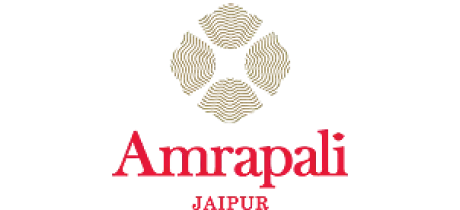
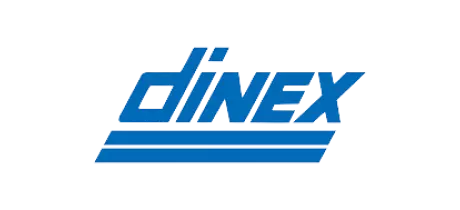
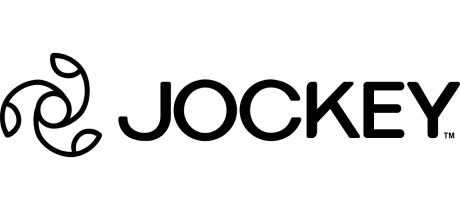
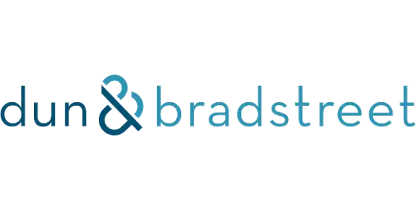
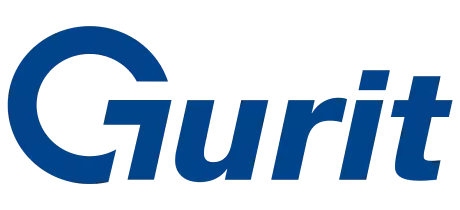
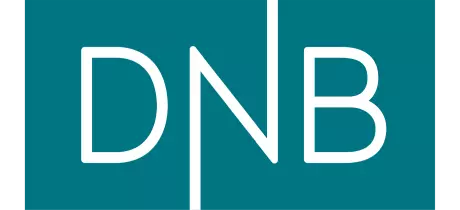
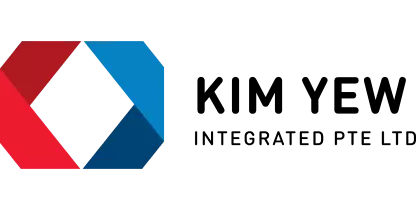
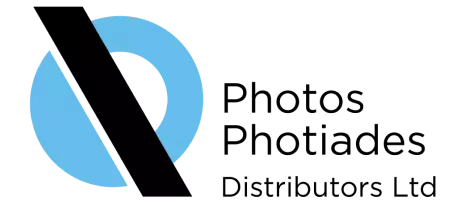
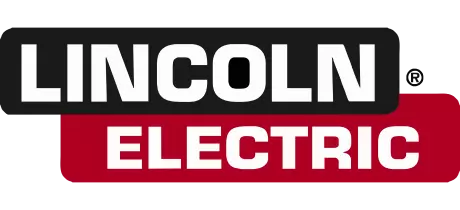
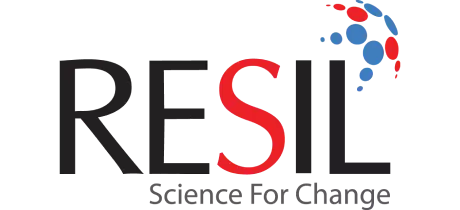
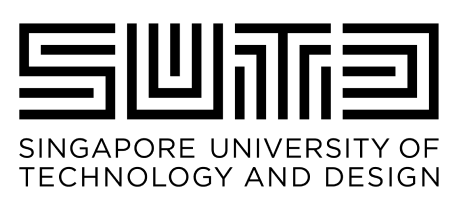
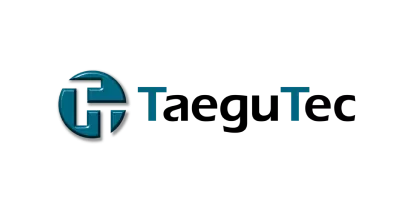
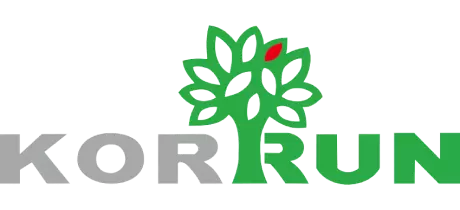
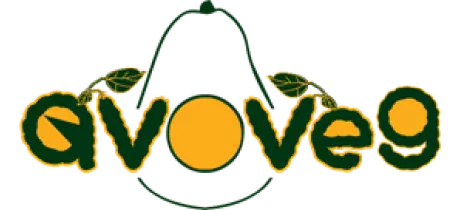
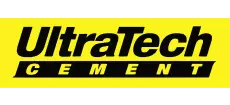
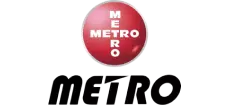
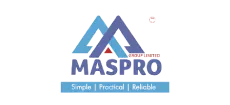
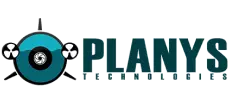
Tired of Unplanned Downtime & Spreadsheet Chaos? Get a Grip on Your Assets with Powerful Maintenance Management Software. Our intuitive platform helps you streamline work orders, optimize preventive maintenance schedules, and gain real-time insights into your equipment performance - so you can reduce costs, extend asset life, and eliminate downtime headaches.
Cryotos empowers your business to move from reactive repairs to a proactive maintenance strategy, maximizing asset uptime and boosting your bottom line. Here's how Cryotos maintenance system delivers tangible benefits:
Say goodbye to unexpected breakdowns and costly downtime. Cryotos Maintenance management software empowers you with the following:
Preventive Maintenance Scheduling: Shift from reactive to proactive by scheduling routine inspections and tasks. This will keep your equipment running smoothly and extend its lifespan.
Early Issue Detection: Leverage sensor data and real-time monitoring to identify potential problems before they escalate into major breakdowns, minimizing downtime and lost productivity.
With Cryotos Maintenance Management System, avoid the paper trail and embrace a digital workflow:
Automated Work Order Creation: Trigger work orders automatically based on equipment schedules, technician availability, or even sensor data, ensuring timely maintenance.
Real-Time Tracking and Communication: Track work order progress at a glance, receive instant updates from technicians in the field, and keep everyone in the loop with seamless communication.
Understand your equipment's performance like never before:
Improved Asset Utilization: Track equipment usage, identify underutilized assets and optimize deployment for maximum efficiency and return on investment.
Extended Asset Lifespan: Proactive maintenance and detailed performance tracking help you extend the life of your equipment, reducing the need for costly replacements.
Accurate Inventory Management: Gain real-time visibility into your spare parts inventory, track stock levels, and automate replenishment to avoid costly delays and production stoppages.
Reduced Carrying Costs: Optimize inventory levels based on usage data and minimize waste by ensuring you have the right parts on hand when needed.
Powerful Reporting and Analytics: Gain valuable insights into your maintenance operations with detailed reports on equipment performance, work order history, maintenance costs, and more.
Identify Trends and Improve Strategies: Leverage data analysis to identify recurring issues, optimize maintenance schedules, and make informed decisions that drive continuous improvement.
On-the-Go Access via Mobile Devices: Give your technicians real-time access to work orders, equipment history, manuals, and communication tools – all from their smartphones or tablets.
Increased Efficiency and Accountability: Improve technician productivity, reduce travel time, and ensure accountability with mobile time tracking, digital signatures, and real-time updates.
Connect with Existing Systems: Integrate your maintenance software with your existing ERP, CMMS, or other business systems for a streamlined workflow and seamless data exchange.
Eliminate Data Silos: Break down data silos by connecting different departments and systems, fostering better collaboration and more informed decision-making.
Single Source of Truth: Manage all your maintenance activities, from work orders to inventory, within a centralized platform, providing a clear overview of your operations.
Simplified Communication: Facilitate seamless communication between technicians, managers, and other stakeholders, keeping everyone on the same page and improving collaboration.
Drag-and-Drop Scheduling Interface: Effortlessly schedule and assign work orders to technicians based on availability, skill set, and location, optimizing resource allocation.
Automated Reminders and Notifications: Reduce missed appointments and improve schedule adherence with automated reminders and notifications for upcoming tasks.
Ensure Regulatory Compliance: Maintain detailed records of maintenance activities, inspections, and certifications to ensure industry standards and regulations compliance.
Reduce Risks and Liabilities: Minimize the risk of accidents, equipment failures, and costly downtime with proactive maintenance and accurate record-keeping.
Experience the power of preventive maintenance scheduling, streamline work order processes for seamless task assignment, and optimize asset performance with comprehensive asset and equipment tracking capabilities. These features are listed below.
Moving beyond reactive repairs to a proactive maintenance strategy maximizes asset lifespan, minimizes downtime, and keeps operations running smoothly. Cryotos Maintenance Management Software empowers you to do just that with robust preventive maintenance (PM) features built for flexibility and efficiency.
Pre-built Templates & Customization: Cryotos offers pre-loaded PM schedules for common assets, or you can easily tailor them to your exact requirements using our intuitive calendar interface.
Effortless Rescheduling & Updates: Need to adjust a PM task? Simply drag and drop it to a new date. Cryotos makes it easy to keep your maintenance plan agile and responsive to changing needs.
Automated Alerts, Never Miss a Beat: Stay ahead of the curve with automatic notifications for upcoming maintenance tasks. Set your preferred frequency—daily, weekly, monthly, bi-monthly, yearly, or even every 5 years—and ensure no critical task falls through the cracks.
Flexible Scheduling for Every Scenario: Cryotos accommodates static and dynamic PM schedules. Define fixed intervals for routine maintenance or leverage dynamic scheduling triggered by usage (e.g., operating hours, mileage) or elapsed time.
Streamlined Task Assignment and Approvals: Ensure accountability with a multi-level approval process. Planners, supervisors, and technicians can be seamlessly integrated into the PM workflow, ensuring tasks are assigned and executed efficiently.
Cryotos maintenance management system empowers you with robust work order management tools designed to streamline operations and maximize efficiency. Here's how Cryotos transforms your workflow:
Easily filter work orders by technician, location, due date, status, and priority. This granular control provides an organized overview of all active, pending, and completed tasks within your operation.
With Cryotos' automated work order generation, manual data entry and the potential for errors are eliminated. Tasks are instantly dispatched, and mobile push notifications are sent directly to assigned technicians, ensuring prompt action and reducing downtime.
Empower your technicians with comprehensive work order details. Attach PDFs, photos, and even videos to provide all the information they need to complete tasks accurately and efficiently the first time around.
With Cryotos' visual calendar interface, you can gain a complete picture of your team's workload. Schedule and track preventive maintenance and ad hoc requests, ensuring balanced workloads, timely completion, and proactive asset management.
With Cryotos Maintenance Solution, equipment failures are a thing of the past. Our Predictive Maintenance harnesses advanced data analysis tools, meticulously detecting anomalies in equipment and operations long before they pose a threat. It's more than just identifying issues; it's about providing clear solutions. Armed with this invaluable data, you can proactively address glitches, ensuring smooth operations and averting costly downtimes.
Why react when you can predict? With Cryotos, you're always ten steps ahead, turning potential challenges into seamless efficiency. Invest in precision, foresight, and unparalleled operational excellence. Choose Cryotos and redefine the future of your equipment care.
Automatically generate a work order, assign it to the appropriate technician based on their skill set and availability, notify them via their mobile device, and even order the necessary parts from your preferred supplier without any manual intervention. Here's how Cryotos makes this possible via the workflow automation feature:
Visual Workflow Builder: No coding required! Our intuitive drag-and-drop interface allows you to easily design, modify, and deploy automated workflows tailored to your needs.
Conditional Logic: Build intelligence into your workflows. Define triggers and actions based on pre-set conditions, ensuring the system adapts dynamically to changing situations and real-time data.
Automated Notifications and Approvals: Keep everyone in the loop and eliminate bottlenecks. Cryotos automatically routes tasks and approvals electronically, providing a clear audit trail for enhanced accountability.
Integration with Other Systems: Cryotos seamlessly integrates with your existing ERP, CMMS, and other enterprise systems, facilitating data synchronization and automated actions across platforms.
Dive into the next-gen of maintenance management where your equipment doesn't just operate; it converses. With IoT devices seamlessly integrated into Cryotos Maintenance Management Software, monitor intricate details like temperature, pressure, and humidity in real-time. Anomalies? Cryotos instantly flags them, autonomously generating work requests. Post validation, it swiftly translates into a corrective work order.
The result? A proactive stance that preempts equipment failures, drastically reducing downtimes. Elevate your maintenance game with Cryotos – where technology meets foresight, ensuring your assets stay a step ahead. Embrace the future today.
Real-Time Asset Tracking: This enables real-time asset tracking for technicians in the field. They can view asset details, check maintenance history, and track asset performance metrics directly from their mobile devices.
Efficient Communication and Collaboration: Effective communication and collaboration are essential for successful maintenance operations. Cryotos Mobile App feature facilitates seamless communication between technicians and team members through instant messaging and notifications.
Mobile Inspections and Data Capture: Enables technicians to inspect and capture data using mobile devices. They can record equipment readings, add photos, and document observations directly within the app.
Data Synchronization and Seamless Integration: Ensures data synchronization between the mobile app and the centralized system. Updates made by technicians in the field are seamlessly synchronized with the main database, ensuring real-time data availability for all stakeholders.
With our comprehensive range of services, Cryotos is committed to not only providing a powerful maintenance management software solution but also supporting your organization every step of the way. From seamless implementation to personalized training, robust APIs for integration, and reliable customer support, Cryotos ensures that your maintenance operations are streamlined, efficient, and optimized for success. Embrace our services and unlock the full potential of streamlined maintenance operations with Cryotos.
We understand that each organization has unique requirements and workflows. That's why our implementation process goes beyond a one-size-fits-all approach. Here's how we ensure Cryotos maintenance software becomes an integrated part of your maintenance ecosystem:
Expert Guidance: Transitioning to new software can feel daunting. Our experienced team provides personalized support throughout the entire implementation journey. We'll answer your questions, address concerns, and provide proactive guidance to guarantee a smooth and efficient onboarding experience.
Custom Configuration: We tailor Cryotos to mirror your specific needs. From configuring preventive maintenance schedules to setting up user roles and permissions, we ensure the software aligns perfectly with your existing workflows, maximizing efficiency from day one.
Seamless Data Migration: Migrating your existing data shouldn't be a roadblock. We handle the secure and accurate transfer of your valuable asset information, including:
Equipment Profiles: Complete historical data, maintenance logs, and associated documentation for all your assets.
Work Orders: Transfer ongoing work orders, their status, assigned technicians, and associated notes.
Inventory Management: Seamlessly migrate your spare parts inventory, including stock levels, reorder points, and vendor details.
You've invested in Cryotos maintenance software to streamline your maintenance operations, but it is only as powerful as the people using it. That's why Cryotos offers comprehensive training programs designed to empower your team and maximize your ROI.
Interactive Video Tutorials: Forget dry manuals and lengthy presentations! Our engaging video modules break down key features and functionalities of Cryotos maintenance scheduling software into bite-sized, easily digestible pieces. Learn at your own pace, pause, rewind, and revisit concepts whenever you need a refresher.
Detailed Documentation: For those who prefer a more traditional approach or need a quick reference guide, our downloadable and searchable user guides offer in-depth information and step-by-step instructions on every aspect of the software. Quickly find the answers you need and troubleshoot issues efficiently.
Interactive Walkthroughs: Experience Cryotos maintenance software in action with our live online sessions led by expert trainers. Get hands-on experience, ask questions in real time, and receive personalized guidance tailored to your specific needs.
On-Site Training: We believe in going the extra mile. For a truly immersive learning experience, we offer on-site training at your location. This personalized approach allows us to tailor the content to your specific workflows and equipment, ensuring your team is confident and comfortable using Cryotos maintenance software from day one.
Cryotos offers an open REST API interface with proper authentication that simplifies the process of integrating and exchanging data across ERP & third applications. This API enables different software programs, like (SAP, Salesforce, and PeopleSoft.) to interact with CMMS Systems without hiccups, allowing efficient data sharing across multiple platforms.
Our dedicated support team acts as an extension of your own, providing the guidance and assistance you need when you need it. Here's how Cryotos support elevates your maintenance management:
Unwavering Availability: We understand that maintenance issues don't adhere to a 9-to-5 schedule. That's why our support team is available 24/7 to answer your questions and address any challenges, no matter the hour.
Choose Your Channel: Whether you prefer the directness of a phone call, the detailed documentation of email, the real-time interaction of live chat, or the convenience of online messaging, we offer a support channel that fits your style.
Industry-Leading Expertise: Our team goes beyond basic troubleshooting. We're seasoned industry experts who understand the complexities of maintenance management across various sectors. We provide proactive guidance and tailored insights to maximize the value of Cryotos maintenance management.
Empowering Knowledge Base: Our comprehensive online knowledge base puts you in the driver's seat. Access a wealth of articles, tutorials, FAQs, and troubleshooting guides at your fingertips.
Maintenance Management Software is a specialized software solution designed to streamline and optimize maintenance operations in various industries. It provides tools and features that assist in scheduling, tracking, and managing maintenance tasks, work orders, assets, inventory, and other maintenance-related activities. It aims to improve operational efficiency, reduce downtime, increase equipment reliability, and enhance maintenance performance.
Cryotos Maintenance Management Solution revolutionizes maintenance operations by offering a comprehensive suite of features and functionalities. It enables businesses to streamline work order management, schedule preventive maintenance, track assets, and equipment, manage inventory, generate insightful reports, and facilitate efficient communication and collaboration among team members. With Cryotos, businesses can automate repetitive tasks, prioritize maintenance activities, optimize resource allocation, improve asset performance, and enhance decision-making for streamlined and efficient maintenance operations.
There is no single answer to this question, as the best maintenance software for one organization may be better for another. However, there are some factors to consider when choosing a CMMS, such as the size and complexity of your operations, the features and functionality you need, and your budget.
Choosing Cryotos as your maintenance management software has numerous benefits. Some of them are below,
1. Improved communication and coordination among maintenance staff.
2. More efficient and effective use of resources.
3. Reduced downtime and increased equipment availability.
4. Improved safety and compliance.
5. Greater visibility into maintenance operations.
Cryotos is available as a cloud-based solution; This makes it flexible to access from anywhere while also giving the added benefit of security for sensitive data.
The CMMS implementation process works by first creating a master database of all the equipment and assets in the company. This master database is then used to create work orders and maintenance schedules. Once the work orders and maintenance schedules are created, they are then assigned to the appropriate staff and technicians.
Cryotos Software caters to various types of maintenance tasks across industries. It supports both reactive and proactive maintenance approaches. Some common maintenance tasks that can be managed with Cryotos include
Preventive Maintenance: Cryotos helps schedule and manage regular maintenance tasks to prevent equipment failures and minimize downtime; This includes inspections, lubrication, calibration, and routine servicing.
Corrective Maintenance: Cryotos assists in managing unplanned or reactive maintenance tasks that arise from unexpected breakdowns or failures. It enables efficient work order creation, assignment, and tracking to resolve issues promptly.
Predictive Maintenance: Cryotos facilitates predictive maintenance strategies by integrating sensors and data sources to monitor equipment health and performance. It enables businesses to track condition-based metrics, set thresholds, and trigger maintenance activities based on predictive analytics.
Asset Management: Cryotos allows businesses to track and manage their assets throughout their lifecycle; This includes recording asset details, maintenance history, warranty information, and tracking asset movements or transfers.
Inventory Management: Cryotos provides features to manage spare parts, tools, and supplies. It allows businesses to track inventory levels, set reorder points, and receive notifications for low-stock items, ensuring the availability of necessary resources for maintenance tasks.Cryotos Software offers a flexible and comprehensive solution that caters to a wide range of maintenance tasks, empowering businesses to streamline their maintenance operations effectively.
I recently purchased Cryotos CMMS Software for asset management needs at my organization and after a few months of testing and monitoring, I'm incredibly pleased with the results. The software is user friendly, accessible and the design is very intuitive. It covers all the aspects of managing maintenance and repair, starting from preventive maintenance and standardizing operation cycles, to scheduling and streamlining workflows. I am highly satisfied with the performance and the range of features offered by Cryotos. Highly recommendable!
Read Review in G2Since we've started using Cryotos, our team has been able to stay on top of all the various SOPs. Checklists and safety procedures are now easily accessible to everyone, and we can quickly reference them whenever we need to. The software has definitely helped to improve our team's communication and efficiency. Plus, the fact that it's cloud-based means we can access it from anywhere, which is a big plus. It has been a great help in keeping everyone on the same page and up to date with the latest procedures.
I am using this application right now for my service team, very good, user friendly, have lot of customisation in workflow and service reports. the team supported for initial implementation, They have good support team. Myself fully recommended this application.
Read Complete Review in G2