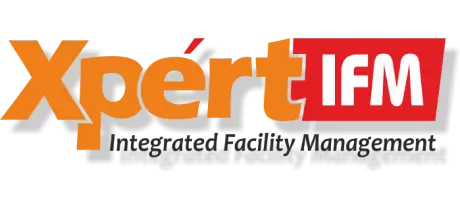
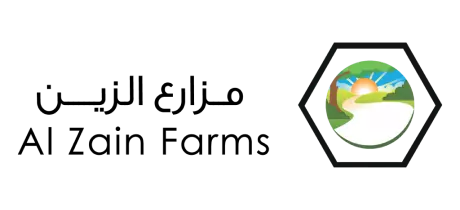
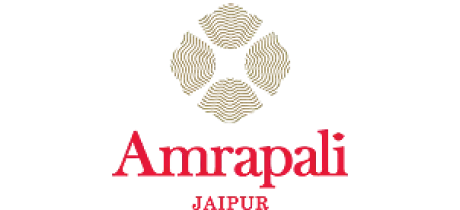
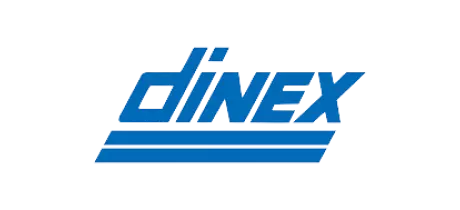
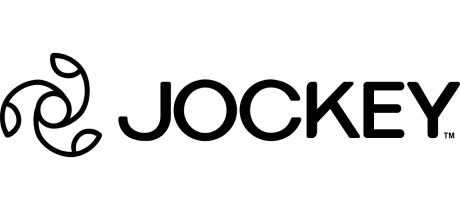
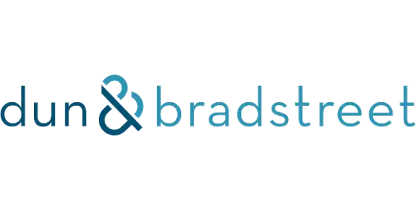
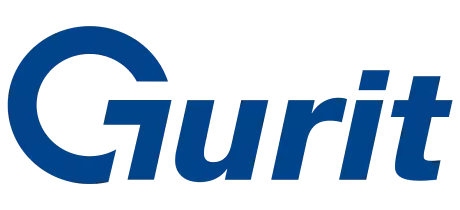
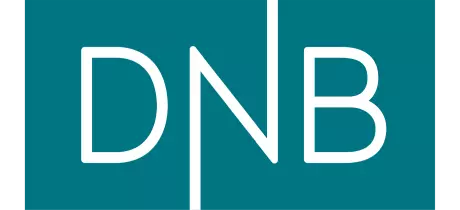
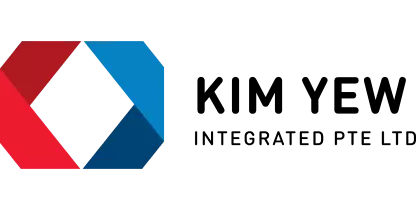
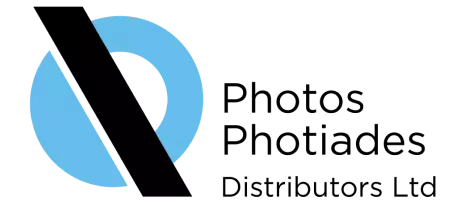
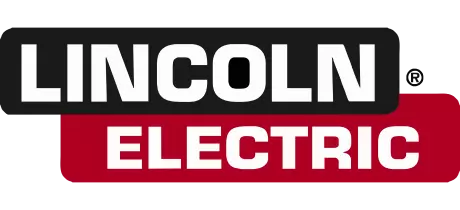
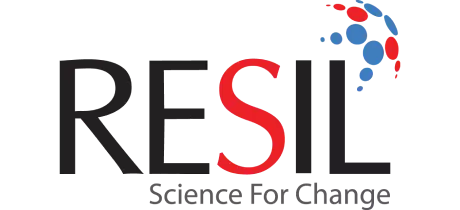
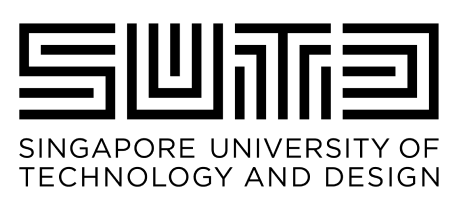
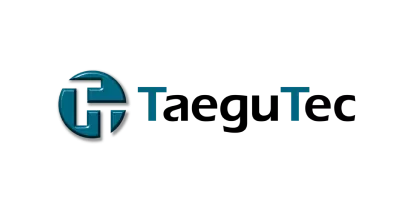
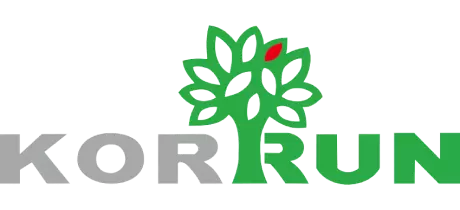
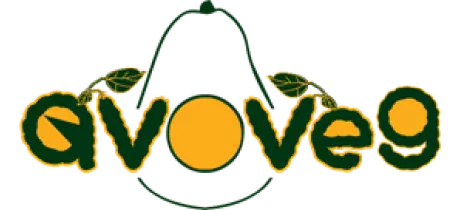
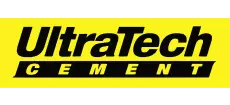
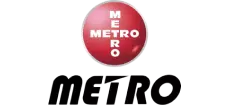
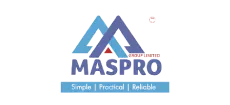
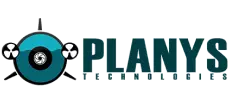
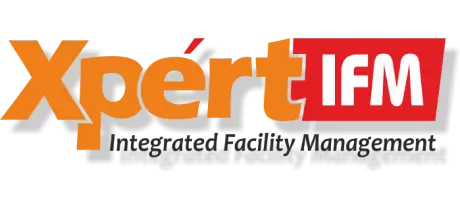
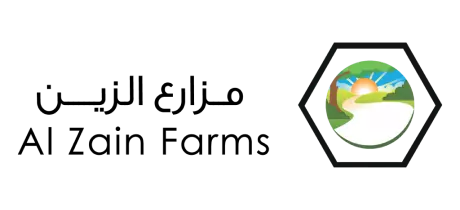
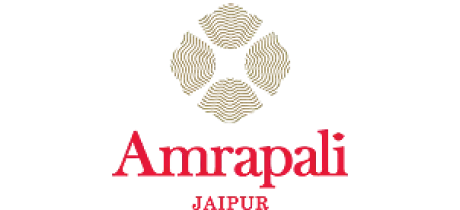
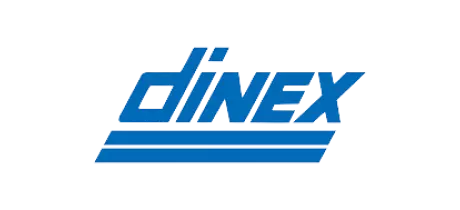
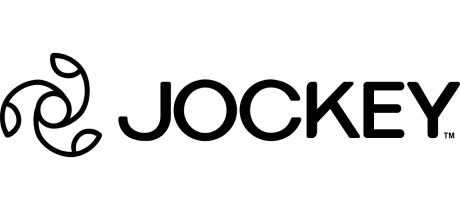
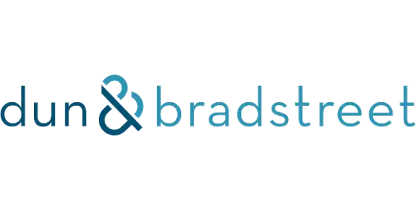
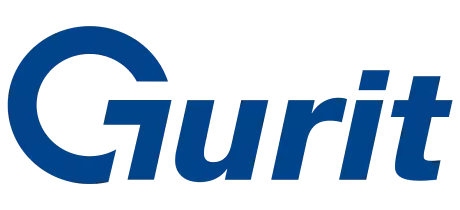
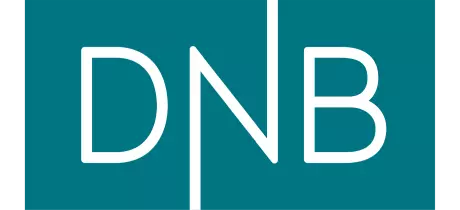
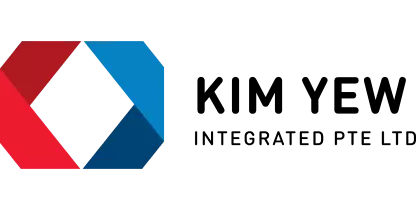
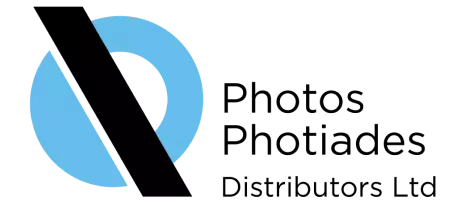
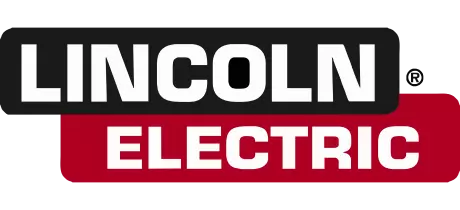
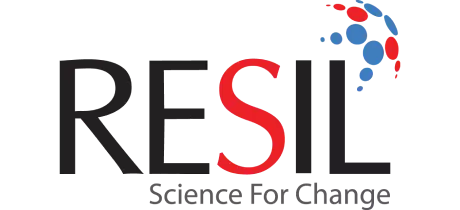
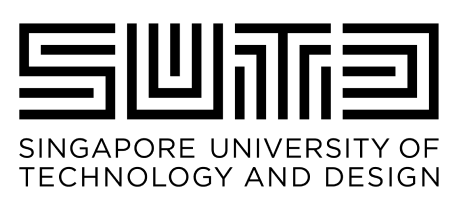
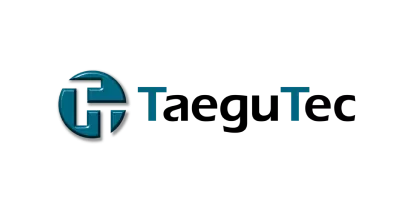
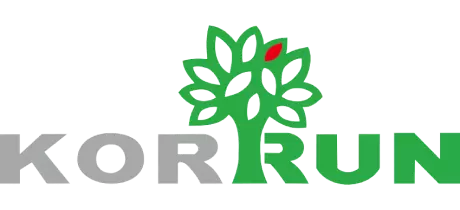
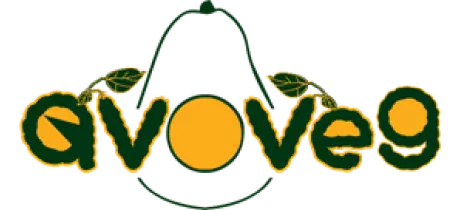
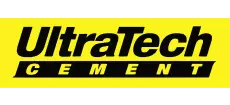
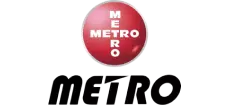
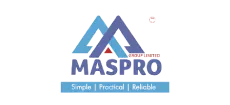
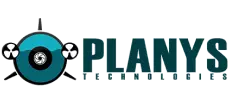
Effortlessly manage preventive maintenance (PM) tasks, track parts inventory, and streamline work orders – all within an intuitive, user-friendly interface that minimizes screen time.
Eliminate spreadsheets! Streamline work order management specifically for Food and Beverage production. Effortlessly create, assign, and track work orders for preventive maintenance (PM) tasks, equipment repairs, sanitation procedures, and compliance checklists.
Assign work orders based on technician skillsets and real-time availability. Ensure the most qualified person handles critical repairs, minimizing downtime and maximizing efficiency.
Pre-built templates for sanitation procedures, calibration checks, and CIP (Cleaning In Place) tasks save you time and ensure consistency.
Ensure accountability and simplify record-keeping with electronic signatures for work order completion.
Move beyond chasing breakdowns and embrace preventive maintenance with Cryotos CMMS. Schedule critical maintenance tasks like equipment cleaning, calibration checks, and belt replacements based on manufacturer recommendations and industry best practices.
Easily track upcoming tasks, monitor completion records, and ensure compliance with regulatory requirements and internal quality standards.
Identify potential equipment issues early with automated reminders and predictive maintenance insights. Prevent costly downtime and maximize the lifespan of your critical production equipment.
Ensure your maintenance team always has the critical parts they need when they need them. Cryotos CMMS provides a streamlined inventory management system for the fast-paced Food & Beverage industry.
Easily track part location, quantity, and minimum reorder levels to prevent costly downtime due to stockouts.
Analyze inventory usage data and predict upcoming needs based on scheduled PM tasks and equipment usage patterns.
Receive automatic alerts when parts reach reorder points. Optimize your inventory levels to minimize overstocking and avoid costly storage expenses.
Automate repetitive tasks like work order generation for sanitation procedures, calibration schedules, and equipment inspections.
Set up automated triggers based on real-time data. For example, it automatically generates work orders when sensor readings indicate a potential equipment issue or trigger preventive maintenance tasks when equipment reaches predefined usage thresholds.
Schedule routine maintenance tasks automatically to ensure critical procedures are completed on time, every time. Minimize compliance risks and maximize equipment uptime.
Revolutionize your maintenance strategy with Cryotos CMMS' integrated IoT meter reading. Eliminate manual data collection and gain real-time insights into the health of your critical Food & Beverage equipment.
Cryotos CMMS analyzes sensor data against predefined industry benchmarks. Automatically detect even minor anomalies that could signal potential equipment issues. Prevent breakdowns before they happen and minimize downtime risks.
Receive instant notifications when sensor readings deviate from normal operating ranges. Empower your maintenance team to assess the situation quickly and take proactive steps to address potential problems.
Gain valuable insights from historical sensor data trends. Identify areas for further optimization of your maintenance program and maximize equipment performance.
Cryotos CMMS Software provides the tools food and beverage industries require to optimize maintenance, minimize downtime, and maximize production efficiency.
Implement proactive maintenance strategies like preventive maintenance (PM) to prevent equipment failures before they disrupt production.
Streamline work order management to ensure maintenance tasks are assigned efficiently and completed quickly.
Gain real-time insights into equipment performance to identify and address potential issues before they escalate into major breakdowns.
Automate sanitation procedures and calibration schedules to consistently comply with strict food safety regulations.
Maintain meticulous documentation of all maintenance activities, facilitating seamless audits and reducing compliance risks.
Track expiration dates for critical spare parts to prevent contamination and maintain the highest quality standards.
Eliminate stockouts with real-time inventory tracking of critical spare parts.
Minimize overstocking by setting reorder points based on historical usage data and predictive maintenance insights.
Streamline the ordering process for spare parts, ensuring maintenance tasks are never delayed due to unavailable parts.
Centralize work order communication in a user-friendly platform, eliminating confusion and ensuring everyone is on the same page.
Facilitate collaboration between maintenance teams, enhancing problem-solving and decision-making.
Empower technicians with real-time access to work order details, equipment manuals, and maintenance history.
Gain valuable insights from equipment performance reports, maintenance cost analyses, and trend data.
Identify areas for improvement in your maintenance program to optimize resource allocation and maximize ROI.
Demonstrate the tangible value of your maintenance efforts to stakeholders with clear and measurable results.
Receive instant push notifications for critical equipment alerts, work order updates, and sanitation schedule reminders. Respond quickly to address issues before they escalate.
Update work orders, record equipment readings, and capture maintenance notes directly within the app. This eliminates data entry errors and ensures accurate record-keeping.
Boost efficiency with intuitive mobile features. Easily access work orders, navigate to equipment locations with integrated maps, and complete tasks faster.
Collaborate effortlessly with technicians and managers in real-time through the app. Share updates, assign tasks, and solve problems from anywhere on the production floor.
CMMS (Computerized Maintenance Management System) software for the Food and Beverage industry is a specialized tool designed to manage and optimize maintenance operations within the sector. It helps businesses streamline work order management, preventive maintenance, inventory tracking, and compliance with food safety regulations, all through an intuitive, user-friendly interface. This software aims to reduce downtime, increase ROI, extend asset lifespan, and decrease repair times, ensuring that food and beverage production facilities run smoothly and efficiently.
Yes, our CMMS software is designed to integrate seamlessly with various systems and platforms commonly used in the Food and Beverage industry. This includes ERP (Enterprise Resource Planning) systems, quality management systems, and production tracking tools. Integration capabilities ensure data flows smoothly between systems, enhancing efficiency and providing a unified view of operations.
Absolutely. Our CMMS software is scalable and can be tailored to meet the needs of small to medium-sized enterprises (SMEs) in the Food and Beverage industry. It offers flexibility regarding features and pricing, ensuring that SMEs can effectively manage their maintenance operations, improve efficiency, and comply with food safety standards without significant upfront investment.
Our mobile CMMS app brings maintenance management right to your team's fingertips, enhancing efficiency and responsiveness. With features like instant push notifications for equipment alerts, work order updates, and the ability to update work orders and capture maintenance notes on the go, the app ensures that your maintenance team can respond quickly to issues, access critical information anytime, anywhere, and complete tasks more efficiently.
We provide comprehensive support to ensure your success with our CMMS software. This includes onboarding and training sessions to get your team up to speed, a dedicated support team available for any queries or issues, and regular updates to the software based on customer feedback and technological advancements. Our goal is to ensure that you maximize the benefits of your CMMS software with minimal disruption to your operations.
I recently purchased Cryotos CMMS Software for asset management needs at my organization and after a few months of testing and monitoring, I'm incredibly pleased with the results. The software is user friendly, accessible and the design is very intuitive. It covers all the aspects of managing maintenance and repair, starting from preventive maintenance and standardizing operation cycles, to scheduling and streamlining workflows. I am highly satisfied with the performance and the range of features offered by Cryotos. Highly recommendable!
Read Review in G2Since we've started using Cryotos, our team has been able to stay on top of all the various SOPs. Checklists and safety procedures are now easily accessible to everyone, and we can quickly reference them whenever we need to. The software has definitely helped to improve our team's communication and efficiency. Plus, the fact that it's cloud-based means we can access it from anywhere, which is a big plus. It has been a great help in keeping everyone on the same page and up to date with the latest procedures.
I am using this application right now for my service team, very good, user friendly, have lot of customisation in workflow and service reports. the team supported for initial implementation, They have good support team. Myself fully recommended this application.
Read Complete Review in G2