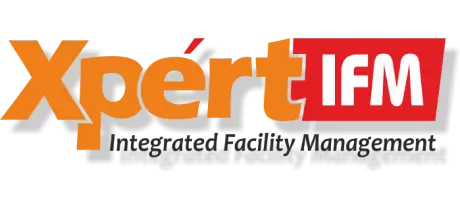
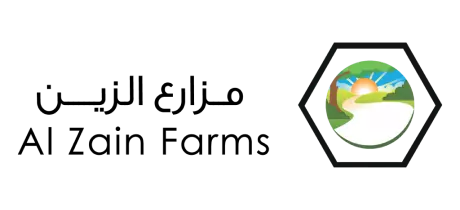
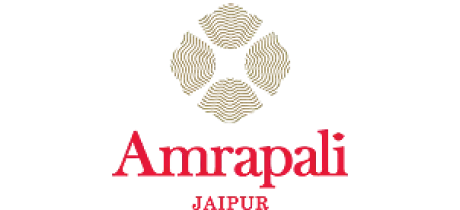
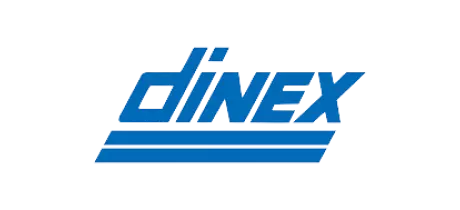
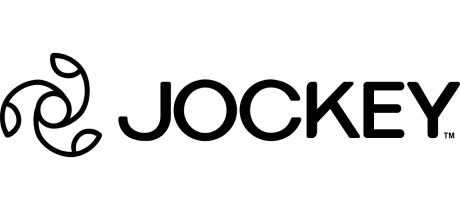
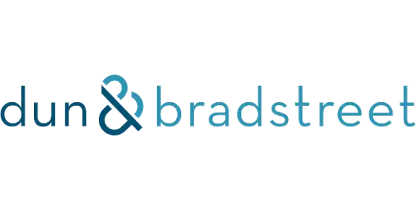
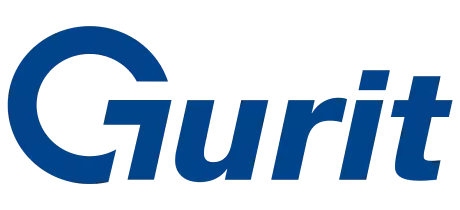
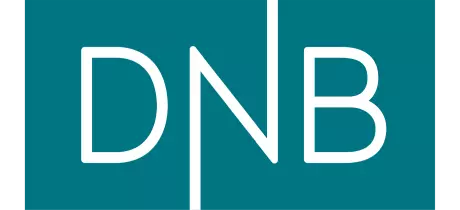
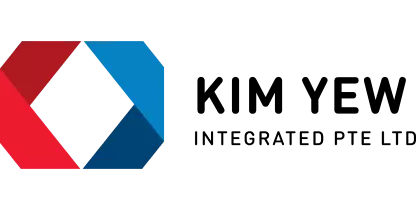
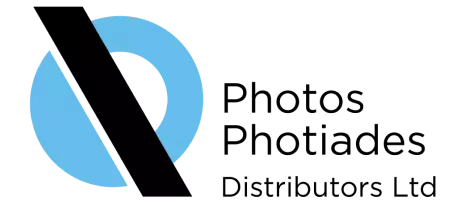
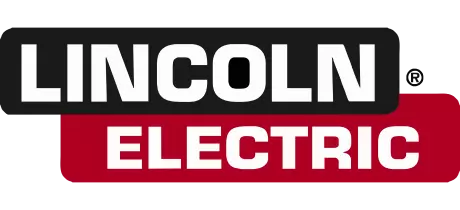
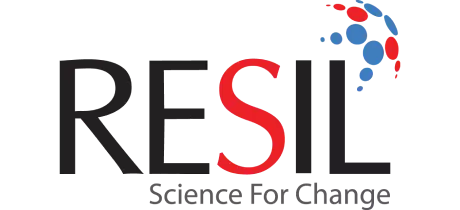
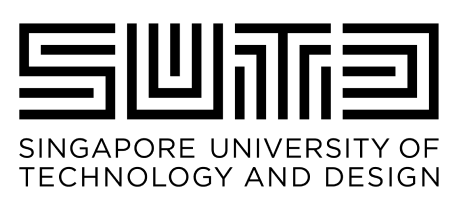
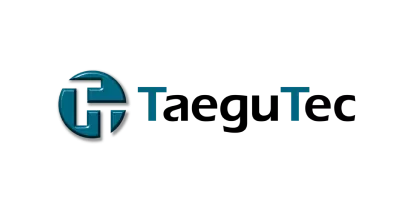
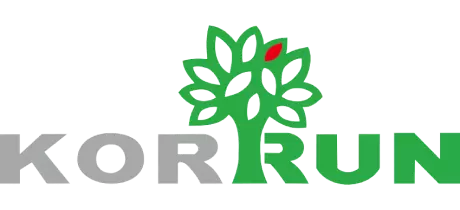
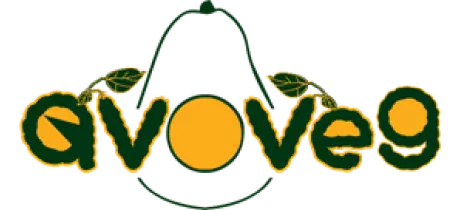
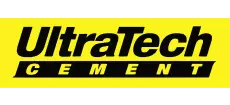
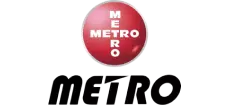
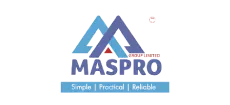
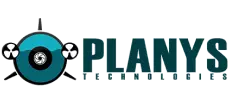
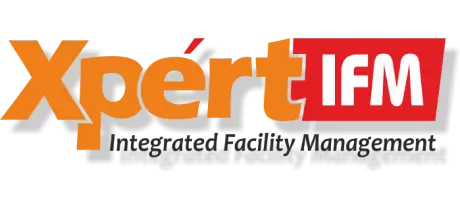
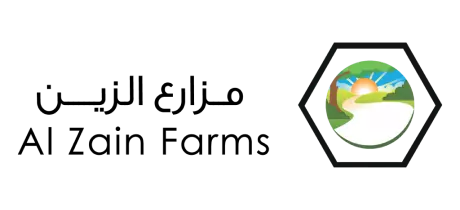
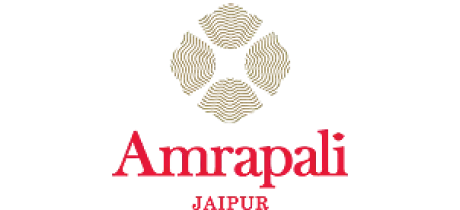
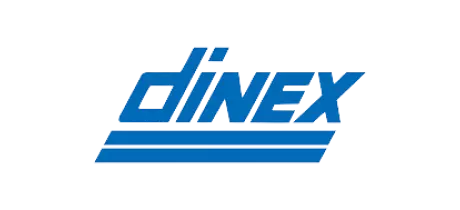
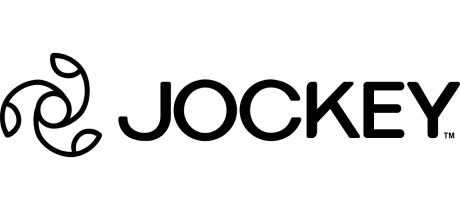
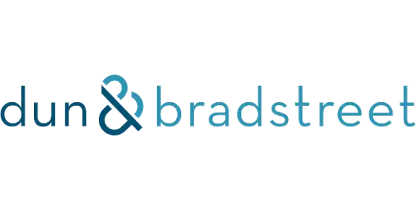
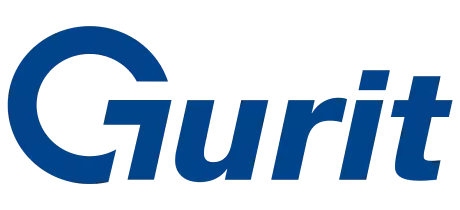
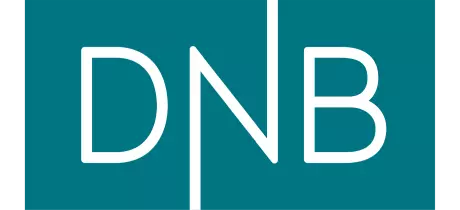
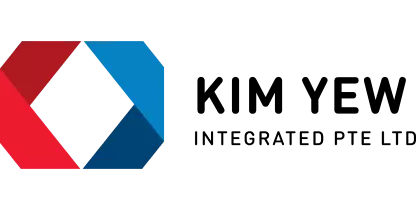
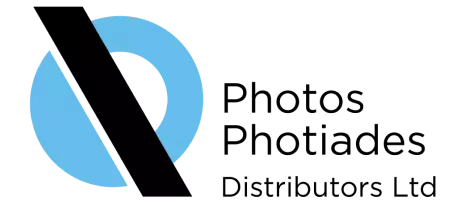
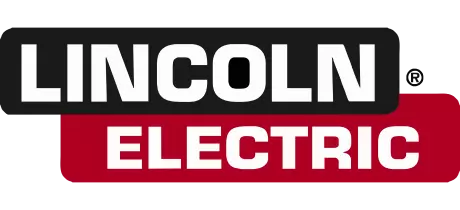
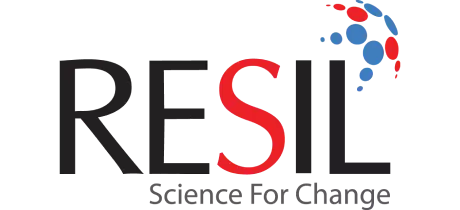
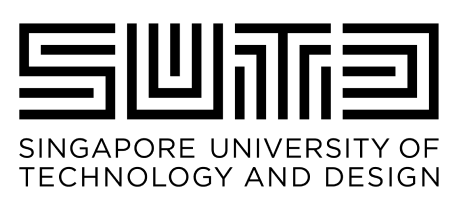
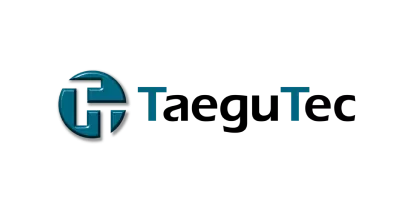
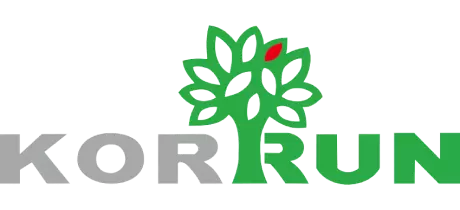
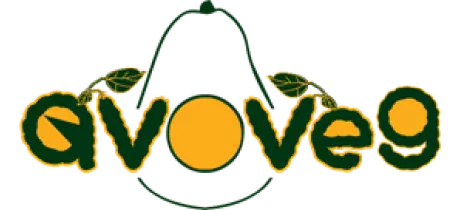
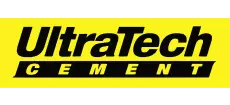
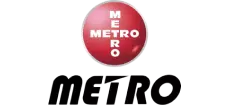
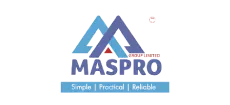
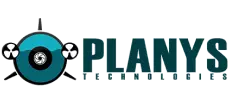
Are you tired of reactive maintenance scrambling to fix breakdowns? Our Heavy Equipment Maintenance Software is the solution you've been waiting for. It's a comprehensive suite of tools designed to streamline your entire maintenance operation, empowering you to maintain your equipment proactively.
Dive deeper into the powerful features designed to optimize maintenance for excavators, loaders, cranes, and your entire heavy equipment fleet. These user-friendly functionalities empower your team to reduce downtime and maximize equipment uptime.
Easily assign work orders to the right team members based on their skills, availability, and location.
Stay on top of every work order with live updates. Watch as tasks move from pending to completed in real-time, ensuring your operations run smoothly without any surprises.
Incorporate equipment inspections, safety checks, and energy efficiency audits directly into your work orders.
Filters work orders based on asset, location, priority, work status, assigned technician, and more.
Gain instant insights into your maintenance operations with customizable dashboards displaying key metrics like work order status, technician performance, and overdue tasks.
Automate PM scheduling and task assignment for your excavators, loaders, cranes, and entire fleet. Ensure the right maintenance gets done at the right time, every time.
Avoid spreadsheets! Set up automated PM schedules based on manufacturer recommendations, operating hours, or customized intervals.
Effortlessly assign PM tasks to the right technicians based on skillset and availability.
To optimize PM schedules for each equipment type, choose from time-based, usage-based, or a combination of both approaches.
Utilize pre-built PM templates for common equipment or create customized schedules for your fleet.
Receive timely push notifications for upcoming PM tasks, keeping your team proactive and preventing missed maintenance.
Maintain a detailed record of every piece of equipment within your fleet. Capture crucial information like make, model, year, serial number, attachments, and purchase details.
Maintain accurate spare parts inventory levels, set reorder points to avoid stockouts, and track part location within workshops or on vehicles.
Track parts used during maintenance activities to identify frequently replaced components and optimize future parts stocking.
Maintain a complete record of all past maintenance activities performed on each piece of equipment. Analyze trends and identify potential problem areas.
Stop guessing, start knowing. Our IoT Meter Reading empowers proactive maintenance for your entire fleet, from dump trucks and graders to crushers and pavers.
Collect critical data like engine hours, fuel consumption, temperatures, and more directly from your heavy equipment using IoT sensors. Gain real-time insights into the health and performance of your entire fleet.
Set custom alerts based on manufacturer recommendations or historical data. Get notified instantly when readings deviate from normal ranges, allowing for early intervention on any equipment, whether a scraper or a reach stacker.
Never miss a potential issue again. Our software automatically triggers work orders when thresholds are breached, ensuring timely repairs and preventing major breakdowns across your entire machinery portfolio.
Transform data into actionable insights. Our robust Reports and analytics empower informed decision-making for your entire heavy equipment fleet.
Maintain a detailed record of all maintenance activities for each piece of equipment, including dates, technicians, work performed, and parts used.
Track and analyze maintenance costs, including labor, parts, and materials. Identify areas for cost reduction and make data-driven decisions to optimize your maintenance budget.
Monitor equipment downtime due to breakdowns or planned maintenance. Gain insights into the impact on productivity and identify strategies to minimize disruptions.
Create interactive dashboards with key performance indicators (KPIs) like MTTR (Mean Time To Repair), MTBF (Mean Time Between Failures), Asset Downtime, and Breakdown Hours. Easily assess equipment health, maintenance costs, and technician productivity at a glance.
Imagine proactive maintenance, clear communication, and reduced downtime for your heavy equipment fleet. Cryotos makes these possibilities a reality.
Automated scheduling with reminders ensures preventive maintenance is completed on time. No more scrambling to remember which excavator needs an oil change or when that loader is due for a filter replacement. Cryotos keeps you organized and proactive.
Need details on a specific piece of equipment? Scan its unique QR code with the Cryotos mobile app and instantly access all its maintenance history, parts manuals, and other relevant information. No more digging through mountains of paperwork or relying on memory.
Seamless integration with WhatsApp keeps everyone on the same page. Technicians can receive work order updates, report breakdowns, and collaborate directly through a familiar platform, eliminating communication breakdowns.
Track and manage equipment licenses and permits electronically. Get automatic renewal reminders and ensure your fleet always operates legally and safely.
Reports and analytics provide valuable insights into your maintenance operations. Identify trends, track equipment performance, and make informed decisions to optimize your resources.
Move from a "fix-it-when-it-breaks" mentality to a proactive approach. Cryotos automates scheduling and reminders for preventive maintenance, catching small issues before they become costly downtime events.
Gain real-time insights into equipment health with IoT meter reading. This allows you to anticipate potential problems and take action before they disrupt your operations.
Cryotos helps you optimize your parts inventory. Real-time usage data and reorder point alerts prevent costly shortages and eliminate overstocking, saving you money on parts and storage space.
Streamline technician workflows, improve task allocation, and minimize wasted time with a centralized work order system. Get the most out of your labor force and reduce unnecessary costs.
With data-driven insights from Reports & Analytics, you can identify areas for cost reduction and optimize your maintenance budget, ensuring your resources are allocated effectively.
Eliminate errors and delays with real-time data synchronization. Access the latest work order details, equipment specifications, and inventory levels anytime.
Get technicians to the right place, fast. Utilize integrated map navigation to find equipment locations and optimize travel routes.
Access, update, and complete work orders with ease. View assigned tasks, add notes, capture photos, and submit reports directly from the mobile app.
Foster communication between technicians, supervisors, and maintenance managers through in-app messaging features. Clarify work order details, request assistance, and share updates instantly.
Protect sensitive data with secure login options utilizing fingerprint or facial recognition technology.
Heavy equipment maintenance software like Cryotos helps you move from reactive repairs to proactive maintenance, preventing costly downtime and keeping your entire fleet – from bulldozers to graders – running smoothly on schedule.
Imagine this: Your technicians have all the work order details for your cranes and pavers at their fingertips on their mobile devices. Parts management for essential components across your entire fleet is a breeze. This is the reality with heavy equipment maintenance software.
Focus on features that address your needs: Do you manage a large fleet of dump trucks and need advanced fuel consumption tracking? Or do you have a smaller operation with just a few crushers and require a simpler solution for work order management? Consider the size and complexity of your equipment portfolio.
Look for user-friendly interfaces and mobile accessibility: Your software should be easy for everyone on your team to use, from technicians on-site maintaining scrapers to office managers overseeing the entire fleet's health.
Remember scalability. Choose software that can grow with your business as your fleet expands to include additional equipment types like reach stackers or conveyor belts or your maintenance needs evolve.
Cryotos automates repetitive tasks: Say goodbye to manual scheduling and data entry for everything from excavator oil changes to routine maintenance on your fleet of backhoes. Automated reminders and streamlined workflows free up your team's valuable time to focus on what matters most – keeping your equipment running smoothly.
Optimize parts inventory and eliminate costly mistakes: Cryotos helps you track parts usage and reorder points for everything from air filters for your dozers to engine components for your entire fleet. This translates to less wasted money on unnecessary parts and fewer delays waiting for crucial replacements.
Data-driven decision making for smarter budgeting: Gain insights into equipment performance and maintenance costs across your entire fleet, from loaders to compactors. Cryotos empowers you to identify areas for improvement, optimize resource allocation, and extend equipment lifespan, all leading to financial savings.
I recently purchased Cryotos CMMS Software for asset management needs at my organization and after a few months of testing and monitoring, I'm incredibly pleased with the results. The software is user friendly, accessible and the design is very intuitive. It covers all the aspects of managing maintenance and repair, starting from preventive maintenance and standardizing operation cycles, to scheduling and streamlining workflows. I am highly satisfied with the performance and the range of features offered by Cryotos. Highly recommendable!
Read Review in G2Since we've started using Cryotos, our team has been able to stay on top of all the various SOPs. Checklists and safety procedures are now easily accessible to everyone, and we can quickly reference them whenever we need to. The software has definitely helped to improve our team's communication and efficiency. Plus, the fact that it's cloud-based means we can access it from anywhere, which is a big plus. It has been a great help in keeping everyone on the same page and up to date with the latest procedures.
I am using this application right now for my service team, very good, user friendly, have lot of customisation in workflow and service reports. the team supported for initial implementation, They have good support team. Myself fully recommended this application.
Read Complete Review in G2